The Most Important Warehouse Safety Tips
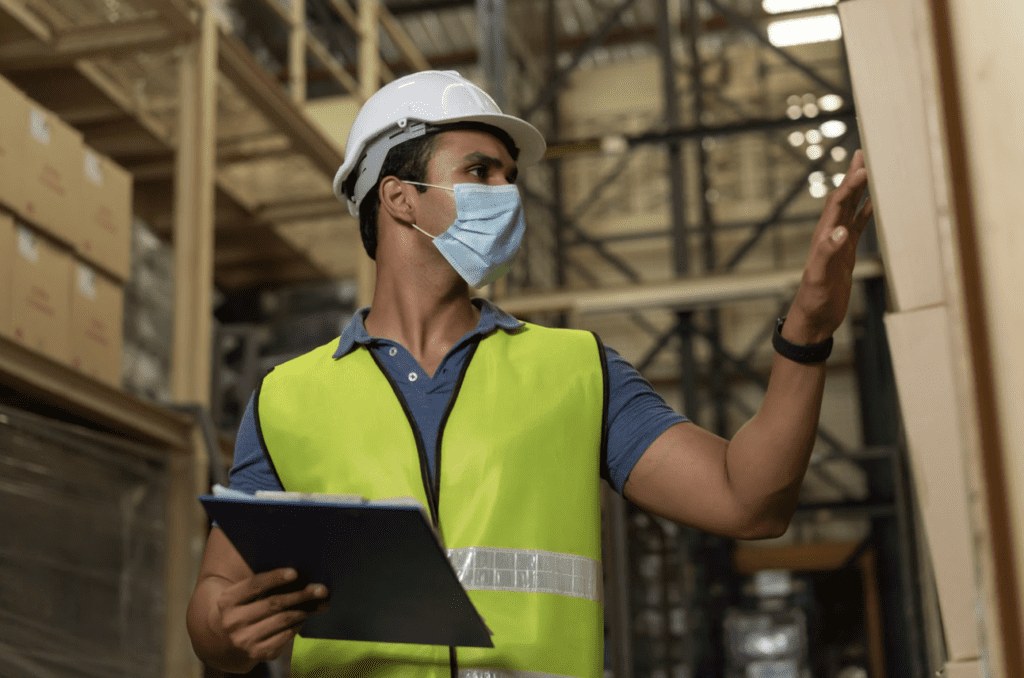
According to the Bureau of Labor and Statistics, warehouse fatalities doubled, and injury rates grew to 5.1 per 100 full-time employees in the past five years. In this period, increased efficiency and automation have led to hurried warehouses. Reviewing warehouse safety tips and regulations can keep your business from adding to these statistics while remaining optimized.
The warehouse includes many dangerous parts to consider. Heavy machinery, increased lifting, and high foot traffic are all factors that increase risk. A few locations amass more risk than other warehouse areas. Most warehouse accidents occur on:
- Docks
- Forklifts
- Conveyors
- Materials storage
- Manual lifting and handling
To keep people in these spaces safe, follow the five most crucial warehouse safety tips below.
Warehouse Safety Tips
- Maintain Warehouse Infrastructure
Though heavy machinery and hazardous materials seem most dangerous, unkempt warehouse infrastructure is an often missed safety hazard. In fact, pallet rack collapses and floor maintenance problems are leading causes of warehouse injuries.
Ensure heavily trafficked spaces undergo an examination on a routine schedule for hazards. Pay attention to floors, load-bearing structures, and materials prone to wear and tear. The items to inspect will quickly add up in a large warehouse, so be sure to create a checklist and calendar for maintenance needs. Some infrastructure pieces include their maintenance schedules as well.
- Catalogue and Label Hazardous Materials
Unsurprisingly, hazardous materials increase risk in warehouses. If incorrectly labeled, the risk of dangerous material injuries increases exponentially. Proper hazardous materials labels should list storage protocol, dangerous chemical interactions, and handling instructions. Be sure to follow OSHA guidelines on labeling, storing, and handling these materials.
Additionally, catalogue which hazardous materials are present in your warehouse so employees can be alerted to their risks. Not all employees may handle hazardous materials, but all employees should be aware of their location and dangerous chemical interactions.
- Ensure Employees Know How to Operate Equipment
As many as 20,000 workers are injured in forklift accidents alone each year. About 5,000 of those injuries occur when forklifts overturn. Forklift falls primarily happen when they are misused. Meaning, 25% of forklift injuries could be prevented with proper equipment operation.
Pieces of advanced or heavy equipment and technology with dangerous parts should require training before use. Catalogue which warehouse machinery requires training and consult the manual or online resources to create a tutorial. Some machinery requires advanced certifications. Be sure to require any licensing mandated by OSHA.
Besides national requirements, in-office regulations keep employees well-trained. Random or short reviews of equipment operations will help prevent injuries as well as preserve equipment.
- Have a Proper First-Aid Kit
Even the most prepared warehouse will incur accidents. Be prepared with a first-aid kit aligned with OSHA standards. Class A OSHA first-aid kits require these 18 supplies:
- Triangular bandage
- Trauma pads
- Sterile pads
- Scissors
- Roller bandage
- Pair exam gloves
- Hand sanitizers
- First aid guide
- Eyewash
- Eye covering
- Cold pack
- Burn treatment
- Gel soaked burn dressing
- Breathing barrier
- Adhesive bandages
- Adhesive tape
- Antibiotic treatment application
- Antiseptic applications
Besides supplies, ensure that as many warehouse workers as possible are first-aid certified as well. Consider Red Cross first aid certification courses as they meet OSHA standards and will help prepare your warehouse employees for the worst.
- Be Consistent
Following warehouse safety tips and tutorials can be cumbersome, but an essential warehouse safety tip is to remain consistent. Most accidents occur when employees complete tasks with regularity. Everyday actions in the warehouse become less fearsome, and mistakes happen due to inattention.
All decisions and actions in a warehouse can lead to safety risks, so consistent training on safety hazards is the goal. Consider adding incentives to safety training as well as interactive formats for optimal output. Large safety organizations will even sponsor appropriate training.
Also important in maintaining safety is allowing proper breaks. Paying attention and adhering to warehouse safety tips and measures requires energy. Proper breaks and following OSHA time regulations will enable employees to remain attentive and follow the rules in the warehouse.
Get More Warehouse Safety Tips From Canal HR
According to the National Safety Council, the average cost of a workplace injury is $38,000. Avoid unnecessary injuries and the costs associated with them by using Canal HR’s risk management services. Canal HR is an experienced professional employer organization that serves businesses across the southeastern region of the United States. Our services help create a safe work environment and keep costs low for our clients. Canal HR’s risk management services include:
- Risk management safety inspections
- Periodic safety training provision
- Workplace and warehouse safety tips and tutorials
- Process and manage workers’ compensation claims
- Handle workers’ compensation hearings
- Investigation into fraud
- Maintain OSHA logs
- Coordination of return-to-work program
When you work with Canal HR, you have a team of HR professionals who specialize in keeping workers safe and employers’ costs low. Let us help you prevent warehouse injuries. Contact Canal HR today!